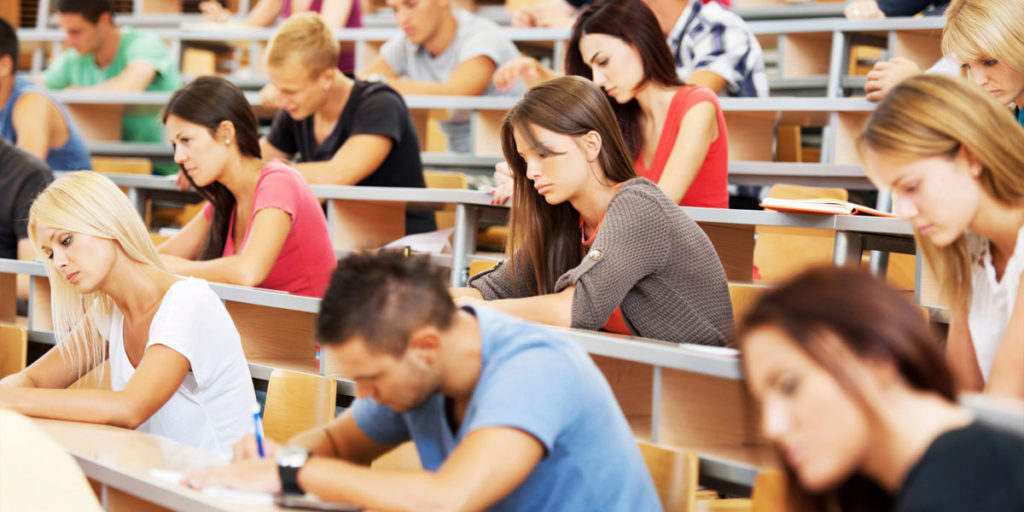
Overview
Curriculum
Overview
The SAP PP (Production Planning) course focuses on the planning, production, and management processes in a manufacturing organization. SAP PP is one of the core modules in SAP ERP, designed to manage production and integrate various production-related processes with other SAP modules like Materials Management (MM), Sales and Distribution (SD), and Finance (FICO). This course is ideal for production planners, production managers, SAP consultants, and professionals working in the supply chain and manufacturing domains.
The course covers all aspects of production planning, from material requirement planning (MRP) to shop floor control, and provides hands-on experience in configuring and managing production processes in SAP.
Course Objectives:
- Understand the key concepts of production planning and control in SAP PP.
- Configure production master data like BOM (Bill of Materials), work centers, and routings.
- Perform material requirements planning (MRP) and production execution.
- Manage production orders, scheduling, capacity planning, and shop floor operations.
- Integrate SAP PP with other SAP modules for end-to-end production and supply chain management.
- Optimize production planning processes for better efficiency and reduced costs.
Curriculum
Module 1: Introduction to SAP and SAP PP Module
- Overview of SAP ERP and its key modules.
- Introduction to SAP PP and its role in the production process.
- Overview of manufacturing processes (discrete, process, and repetitive manufacturing).
- Understanding the integration of SAP PP with other modules (MM, SD, FICO).
- Navigating the SAP PP module and using key transaction codes.
Module 2: Organizational Structure in SAP PP
- Defining and configuring organizational elements (plant, storage location, work centers).
- Understanding production-specific organizational units.
- Mapping organizational structure in SAP PP.
- Assigning roles and authorizations in the production process.
Module 3: Master Data in SAP PP
- Overview of production master data and its importance.
- Creating and managing Bill of Materials (BOM) in SAP.
- Work centers: defining capacities, labor, machine allocation, and cost centers.
- Routing: defining operations, sequences, and work steps for production.
- Production version and alternate BOM.
Module 4: Material Master and Product Lifecycle Management (PLM)
- Understanding the material master and its role in production.
- Creating material master records and managing materials for production.
- Material type, procurement type, and other key parameters.
- Integration of material master with MM and SD modules.
- Overview of SAP PLM and its relevance in production planning.
Module 5: Demand Management
- Introduction to demand management in SAP PP.
- Creating and managing independent and dependent requirements.
- Forecasting and planning strategies in demand management.
- Linking demand management with sales and operations planning (S&OP).
- Transfer of requirements from sales orders to production planning.
Module 6: Material Requirement Planning (MRP)
- Overview of Material Requirements Planning (MRP) in SAP.
- Configuring and executing MRP runs.
- Master production scheduling (MPS) and its role in production.
- Analyzing MRP results and exceptions.
- Managing planned orders, purchase requisitions, and stock levels.
Module 7: Production Orders and Execution
- Overview of production order management in SAP PP.
- Creating, releasing, and scheduling production orders.
- Shop floor control: managing and tracking production operations.
- Material withdrawal and goods movement in production.
- Confirming production orders and backflushing.
Module 8: Capacity Planning and Scheduling
- Understanding capacity planning in production processes.
- Defining work center capacities (labor, machines, etc.).
- Scheduling techniques: forward, backward, and finite scheduling.
- Load leveling and capacity leveling strategies.
- Integration of capacity planning with MRP and production orders.
Module 9: Shop Floor Control
- Managing shop floor activities using SAP PP.
- Monitoring work progress, production confirmations, and material availability.
- Handling production deviations and rework.
- Integrating with quality management for inspection and approval processes.
- Reporting and analyzing shop floor performance.
Module 10: Repetitive Manufacturing and Process Industry
- Overview of repetitive manufacturing in SAP PP.
- Configuring and managing repetitive production processes.
- Product cost controlling and period-end closing for repetitive manufacturing.
- Overview of production planning for process industries (PP-PI).
- Managing recipes, resources, and process orders for process manufacturing.
Module 11: Integration with Other SAP Modules
- Integration of SAP PP with Materials Management (MM) for material planning and procurement.
- Integration with Sales and Distribution (SD) for sales orders and demand forecasting.
- Integration with Finance and Controlling (FICO) for cost tracking and valuation.
- Integration with SAP Quality Management (QM) for quality control during production.
- Overview of SAP Plant Maintenance (PM) integration for equipment and machine maintenance.
Module 12: Production Planning for Discrete Manufacturing
- Understanding discrete manufacturing processes.
- Configuring production planning for make-to-order and make-to-stock scenarios.
- Managing production versions and alternate routings.
- Performing order costing and variance analysis.
- Handling subcontracting and external processing.
Module 13: Reporting and Analytics in SAP PP
- Overview of standard SAP PP reports.
- Generating custom reports for production planning and execution.
- Analyzing production performance, capacity utilization, and work center efficiency.
- Integration with SAP Business Intelligence (BI) for advanced reporting and analytics.
- Real-time monitoring and key performance indicators (KPIs) for production.
Module 14: Advanced Features and Customization in SAP PP
- Configuring and customizing SAP PP for business-specific needs.
- User exits, BADIs, and enhancements in SAP PP.
- Managing variant configuration and configurable materials.
- Optimizing production processes using advanced planning strategies.
- Implementing best practices in production planning and control.
Module 15: Project-Based Learning and Final Assessment
- Hands-on project simulating a real-world production planning scenario.
- Creating production orders, scheduling, and executing production processes.
- Performing MRP, managing work centers, and monitoring shop floor activities.
- Integrating SAP PP with other modules for an end-to-end production flow.
- Final project assessment and feedback.